« Articles/Nathael/Domotab et elec Libre partie4 » : différence entre les versions
(Page créée avec « {{DISPLAYTITLE:Électronique et domotique libre - partie 4 : Un module en vrai, FabLabs et fabrication maison}} <div style="float:left; margin-right: 2.5em;">__TOC__</div>... ») |
|||
Ligne 59 : | Ligne 59 : | ||
Les couches de cuivres sont notées "*.Cu", les couches de vernis épargne sont les "*.Mask", les couches de sérigraphie correspondent aux "*.SilkS" (pour Silk Screen), les couches pour les pochoirs CMS sont les "*.Paste" (pour "Solder Paste", ou "pâte/crème à souder" en français), et les contours du PCB sont sur la couche "Edge.Cuts". | Les couches de cuivres sont notées "*.Cu", les couches de vernis épargne sont les "*.Mask", les couches de sérigraphie correspondent aux "*.SilkS" (pour Silk Screen), les couches pour les pochoirs CMS sont les "*.Paste" (pour "Solder Paste", ou "pâte/crème à souder" en français), et les contours du PCB sont sur la couche "Edge.Cuts". | ||
Pour le reste des cases à cocher, il me semble que les cases cochées par défaut conviennent, sinon reportez vous à la capture d'écran (Figure | Pour le reste des cases à cocher, il me semble que les cases cochées par défaut conviennent, sinon reportez vous à la capture d'écran (Figure à droite). | ||
Il faut ensuite "Tracer" (ce qui génère les fichiers sélectionnés), puis "Créer les Fichiers de Perçage". | Il faut ensuite "Tracer" (ce qui génère les fichiers sélectionnés), puis "Créer les Fichiers de Perçage". |
Dernière version du 2 septembre 2020 à 21:56
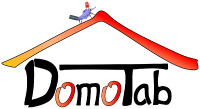
Les trois articles précédents (parus dans les numéros 7 et 8 d'Open Silicium) vous ont présenté la partie conception sur ordinateur d'un module pour le projet DomoTab. Il est maintenant temps de passer de la conception à la réalisation, et de fabriquer le module que nous avons conçu.
Paru dans le numéro 13 du magazine Open Silicium.
Petite vérification
Avant de rentrer dans le vif du sujet, une note pour ceux qui n'ont pas réalisé le schéma proposé dans les articles précédant : vérifiez que vous avez prévu un moyen simple pour accéder à l'interface de programmation du microcontrôleur choisi, si possible un bouton reset, et un moyen permettant de mettre le microcontrôleur en mode programmation si besoin.
Dernière étape sur ordinateur
Les articles précédents nous ont permis de créer le schéma du module GPIO-Demo et de réaliser le routage pour préparer la réalisation des PCB (Printed Circuit Board, ou Circuits Imprimés (CI) en français). Il reste une dernière étape avant la fabrication : la génération des plans de fabrication. Cette étape dépendra grandement de la solution choisie pour la fabrication du PCB. Certains sous-traitants acceptent directement le format natif KiCad, mais ils sont assez rares et la majorité des fabricants acceptent le format Gerber. Cependant si vous souhaitez réaliser vos PCB vous même aucun de ces deux formats ne vous sera utile et nous verrons plus tard comment procéder.
Fichiers Gerber et "layers"
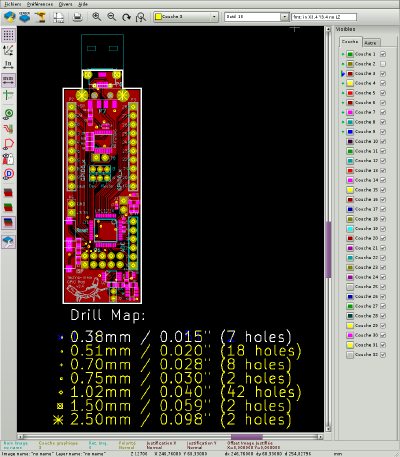
Les plans de fabrication les plus utilisés sont au format Gerber. Il s'agit d'un ensemble de fichiers décrivant chacun une couche ("layer" en anglais) du circuit imprimé final : couches de cuivre, contours, perçages (trous métallisés et trous non métallisés sur deux couches différentes), sérigraphies, vernis épargne, et masques de soudure. Toutes ces couches correspondent aux couches que l'on a sous KiCad (pcbnew), rien de nouveau donc. Cependant, toutes ne seront pas forcément présentes en fonction de votre circuit et de la finition que vous désirez.
Le nombre de couches de cuivre dépendra de ce que vous aurez choisi pour le routage de votre circuit, donc deux couches dans le cas du module que nous avons créé, mais cela peut aller de une seule couche de cuivre, à dix couches pour les circuits les plus complexes et les plus denses. Lorsqu'il y a plus de deux couches la fabrication "maison" sur un seul PCB n'est plus possible, et les prix grimpent.
La couche de contour correspond aux découpes du circuit imprimé. Tous les fabricants n'acceptent pas les découpes complexes, renseignez vous avant de payer si votre circuit comporte des découpes intérieures ou des découpes courbes.
Les couches de perçage correspondent aux trous pour les composants "traversants" et aux vias (pour les trous métallisés) et aux trous de fixation ou de placement de certains connecteurs qui ont des picots de placement en plastique (trous non métallisés). Lorsque vous visualisez les fichiers gerbers sous KiCad (gerbview) les trous sont représentés par des formes géométriques diverses, une par diamètre de perçage, mais les trous auront bien la forme que vous avez définie :)
Les couches suivantes sont optionnelles, mais bien utiles.
Les couches de vernis épargne (dessus et dessous) définissent un masque de vernis qui sera appliqué sur la carte pour recouvrir les zones ne nécessitant pas de soudures. C'est cette couche qui définit la couleur de la carte. Dans certains cas le vernis vert est inclus dans le prix de fabrication, mais les couleurs moins habituelles (rouge, bleu, noir, ...) impliquent un surcoût parfois non négligeable. Cette couche est générée automatiquement à partir des données des empreintes des composants et d'un paramètre global sous KiCad qui se trouve dans le menu Dimensions --> Marge Masque des Pads ([RefCard-5.26]). Dans la majorité des cas il n'est pas nécessaire de laisser de marge supplémentaire, et une valeur de 0 fait l'affaire. Les cas particuliers peuvent être définis dans l'empreinte du composant. L'utilisation des couches de vernis donne un rendu beaucoup plus propre et facilite grandement la soudure des composants CMS.
Les couches de sérigraphie (dessus et dessous) définissent les textes et autres tracés imprimés en blanc (dans la très grande majorité des cas) sur votre PCB. Ces textes vous aideront à placer les composants lors de la fabrication et à repérer les connecteurs ou les broches qui vous intéressent lors de l'utilisation. Bien souvent une seule couche de sérigraphie suffit.
Les masques de soudure (dessus et dessous) servent à la fabrication des pochoirs pour les composants CMS. Ils ne sont nécessaires que si vous désirez faire fabriquer un pochoir métallique en découpe laser. Ce pochoir est très utile si vous avez de nombreux composants CMS, et PCB-Pool le propose gratuitement pour les petites quantités (moins de 100 PCB), mais il est possible de le réaliser dans un FabLab en découpe laser avec une feuille de plastique (voir plus loin).
Génération des fichiers Gerbers
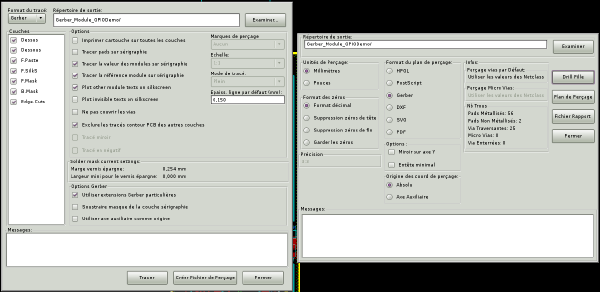
Sous KiCad la génération des fichiers Gerbers se fait via le menu Fichiers --> Tracer ([RefCard-5.27]). KiCad supporte plusieurs types de fichiers, il faut bien sélectionner "Gerber".
Je vous conseille de créer un dossier pour les fichiers gerbers, cela simplifiera la création d'une archive pour envoyer les fichiers au sous-traitant qui fabriquera vos cartes.
Il faut ensuite sélectionner les bonnes couches à inclure dans l'export. Toutes les couches actives dans votre projet se trouvent dans la colonne de gauche, à vous de vérifier que celles qui vous intéressent sont bien cochées.
Les couches de cuivres sont notées "*.Cu", les couches de vernis épargne sont les "*.Mask", les couches de sérigraphie correspondent aux "*.SilkS" (pour Silk Screen), les couches pour les pochoirs CMS sont les "*.Paste" (pour "Solder Paste", ou "pâte/crème à souder" en français), et les contours du PCB sont sur la couche "Edge.Cuts".
Pour le reste des cases à cocher, il me semble que les cases cochées par défaut conviennent, sinon reportez vous à la capture d'écran (Figure à droite).
Il faut ensuite "Tracer" (ce qui génère les fichiers sélectionnés), puis "Créer les Fichiers de Perçage". Pour les fichiers de perçage, il faut bien sélectionner le format Gerber, et cliquer sur "Drill file" et "Plan de perçage". Je ne sais pas si les deux sont utiles, mais j'envoie systématiquement les deux et je n'ai pas eu de problème ni de retour ou remarques, donc je continue comme ça :)
Pour la suite, il ne vous restera plus qu'à faire une archive (zip le plus souvent) pour envoyer votre PCB en fabrication.
Vous pouvez vérifier les fichiers en utilisant l'utilitaire gerbview qui est intégré à la suite KiCad, et qui vous permet d'activer ou désactiver les couches une à une (après les avoir "chargées" une première fois), et ainsi vérifier que vous n'en avez pas oublié une, ou qu'il n'y a pas d'erreur par rapport à ce que vous attendiez (trop de textes sur la couche sérigraphie, plans de masse pas mis à jours, ....)
Version "fait maison" : fichiers SVG
Pour la version fait maison, les fichiers Gerbers ne sont pas utiles, mais KiCad permet l'export au format SVG des différentes couches de fabrication.
L'interface d'export se trouve dans le menu Fichiers --> Export SVG ([RefCard-5.28]). Dans la majorité des cas seules les couches de cuivre sont intéressantes, mais vous pouvez très bien ajouter des guides de placement sur une couche "utilisateur" (Eco*.User) et vouloir les imprimer aussi, ainsi que le contour du circuit, pour faciliter la découpe finale.
De même, compte tenu de la difficulté d'impression de la sérigraphie, vous pouvez imprimer une partie des textes sur la couche de cuivre, ce qui vous permet de disposer de quelques indications supplémentaires sur votre PCB sans devoir jouer du marqueur.
Dans ce cas là, vous pouvez choisir de tout imprimer dans le même fichier, ce qui vous évite de devoir replacer les différents éléments correctement à partir de plusieurs fichiers.
N'oubliez pas de cocher le tracé en miroir, que ce soit pour la technique de l'insolation (pour que l'encre soit au plus près du cuivre et le protège mieux, permettant des tracés plus fins), ou la technique de décalcomanie (voir plus loin).
Vous pouvez ensuite visualiser le résultat avec Inkscape, et éventuellement regrouper plusieurs PCB.
Il est possible de faire des PCB double couche, quelque soit la technique utilisée, mais attention, l'alignement doit être précis, il faudra donc penser à mettre des repères qui permettront de positionner les masques lors de la fabrication. Ces repères peuvent être placés sous KiCad ou sous Inkscape, mais il est préférable de le faire sous KiCad car ils resteront présents si vous faites des modifications, ce qui n'est pas le cas pour la version Inkscape.
Attention : Dans le cas de la fabrication maison de circuits simple couches avec des composants traversants, ceux-ci doivent être placés de l'autre côté du PCB lors du placement des composants sous KiCad pour pouvoir être soudés sur les pistes.
Note : Il est possible, lorsqu'il n'y a que quelques pistes sur la couche de cuivre du dessous, de ne faire qu'un PCB simple couche, et de remplacer les pistes manquantes par des morceaux de pattes de composants ou des fils.
Fabrication du PCB
Home Made et FabLab/ElectroLab
La fabrication maison de cartes électroniques n'est pas très compliquée et peut être à la portée de tous ... ou presque.
Pour ceux qui ont accès à l'Electrolab de Nanterre (http://www.electrolab.fr/), ils vous donneront des indications bien plus précises et détaillées que celles que je pourrais vous donner ici, et surtout, en échange d'une cotisation modique (comme pour tout FabLab) vous aurez accès à du matériel vous permettant de réaliser vos circuits imprimés.
Mais pour le reste de la France ... il faut se débrouiller (renseignez vous tout de même, le FabLab le plus prêt de chez vous a peut-être une partie du matériel, ou sera intéressé pour s'équiper).
Il y a globalement trois techniques pour fabriquer des PCB sans faire appel aux services d'un sous-traitant professionnel : La méthode classique "isolation / révélation", la méthode "décalcomanie", et la méthode usinage.
Les trois méthodes ne diffèrent que par les premières étapes, je détaillerais les étapes suivantes dans la partie "finitions" qui sera commune aux trois méthodes.
Insolation / révélation
Cette méthode nécessite l'utilisation de plaques pré-sensibilisées, que vous allez "graver" en trois étapes. Je n'ai personnellement pas re-testé cette solution, que j'avais mise en œuvre à l'école, car je n'aime pas trop manipuler les produits chimiques dangereux, et que je n'ai pas d'insoleuse UV, mais vous trouverez de nombreux tutoriels sur internet, et je vais vous en présenter rapidement le principe.
La première étape est l'insolation, ou exposition. La plaque de cuivre pré-sensibilisée est recouverte d'un film sensible aux UV. La plaque doit être exposée aux UV à travers un "typon" qui n'est autre qu'une impression du circuit imprimé sur film transparent. Il vous faudra donc disposer d'une insoleuse à UV.
L'étape suivante, la révélation, utilise un premier produit dangereux, la soude, pour dissoudre les parties du film photosensible qui ont été exposées. Attention, j'ai bien dit produit dangereux, utilisation de gants et de lunettes de protection obligatoire.
La troisième étape, la gravure proprement dite, utilise un autre produit dangereux (mais moins) et surtout qui tache définitivement les tissus : le perchlorure de fer. Celui-ci va attaquer le cuivre qui n'est plus protégé par le film photosensible, ne laissant du cuivre que pour les pistes, faisant apparaître le circuit imprimé. Pour accélérer le processus et éviter de gaspiller une grande quantité de produit, il est possible d'utiliser une éponge et de frotter délicatement la surface du PCB avec un coin de l'éponge imbibé de perchlorure de fer. Le film de protection est ensuite retiré avec de l'alcool à bruler (il doit être possible de tester avec de l'acétone ou de l'alcool à 70°).
Décalcomanies
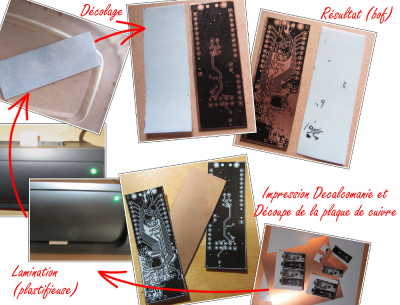
Il existe une première alternative à la solution "classique", qui utilise le principe des décalcomanies.
Cette solution est en deux étapes, et utilise des plaques de cuivre non pré-sensibilisées, une imprimante laser (obligatoire) et une plastifieuse pour la première partie et toujours du perchlorure de fer pour la gravure.
Le dessin de votre carte doit être imprimé sur un papier à décalcomanie (je n'ai testé que celui proposé par "PCB-Fab-In-A-Box" dans leur kit, mais je pense que d'autres font l'affaire), puis transféré à chaud avec une pression régulière sur le circuit imprimé. C'est cette étape qui est critique et qu'il faut parfois reprendre plusieurs fois, surtout si vous ne pouvez pas vous procurer une des plastifieuses spécifiées par "PCB-Fab-In-A-Box", que Amazon refuse de livrer en dehors des États-Unis.
Pour améliorer les résultats, il faut frotter la plaque de cuivre avec une éponge abrasive type "tampongex" (éponges vertes) pour la nettoyer, puis la chauffer à l'aide d'un fer à repasser (attention, elle devient brulante) avant d'y déposer le décalcomanie et de passer le tout dans la plastifieuse. Il est possible de se passer de la plastifieuse, mais le dosage de la pression avec le fer à repasser est alors critique.
Le papier est ensuite décollé en faisant tremper le tout une minute dans l'eau, et si tout c'est bien passé, l'encre est alors déposée sur le cuivre. Si il y a des pistes rompues, ou des parties qui n'ont pas collé sur le cuivre, il est possible de recommencer en enlevant l'encre qui s'est déposée avec de l'acétone.
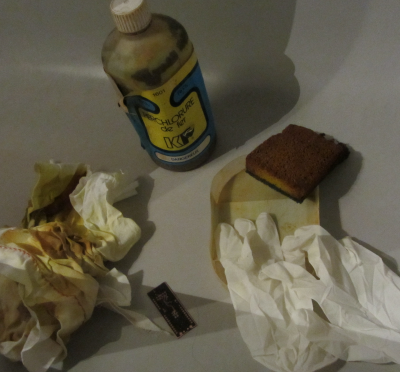
Le site "PCB-Fab-In-A-Box" conseille ensuite d'appliquer une couche de protection à l'aide d'un film plastique (fourni dans leur Kit), mais avec ma plastifieuse je n'ai pas réussi à le déposer correctement, et la gravure se passe très bien sans.
Ensuite il faut procéder à la gravure avec le perchlorure de fer, comme pour la méthode précédente, l'astuce avec l'éponge étant toujours valable.
Cette méthode permet d'obtenir des pistes assez fines, mais nécessite plusieurs essais pour prendre en main la technique d'application des décalcomanies.
Usinage
La troisième méthode utilise une fraiseuse numérique pour retirer le cuivre inutile par gravure mécanique et non plus gravure chimique.
Il vous faut alors transformer votre fichier SVG en tracé de découpe et la machine fait le reste. Il doit être possible de faire percer les vias et autres trous au même moment ou avec un autre outil, mais je n'ai pas pu tester cette solution car les pistes utilisées pour mes PCB ont été jugées trop fines par les personnes disposant d'une fraiseuse qui auraient pu réaliser des essais.
Finitions
Une fois le cuivre gravé, il reste encore deux étapes.
La première étape est optionnelle, il s'agit de l'étamage chimique des pistes. Il suffit pour cela de faire tremper le circuit dans une solution d'étain chimique jusqu'à ce que les pistes aient changé de couleur.
La deuxième étape est le perçage des vias et des différents trous pour les composants. L'utilisation d'une petite perceuse sur colonne permet un travail bien plus efficace et précis, mais reste que les trous des vias ne seront pas métallisés.
La métallisation des trous des vias peut se faire de façon chimique, mais cela demande un peu (beaucoup) de matériel et une installation en conséquence, tandis que la deuxième consiste simplement à utiliser de pattes de composants que vous avez coupées lors de l'assemblage d'un autre circuit pour relier les deux côtés du circuit imprimé en les soudant de chaque côté sur les pastilles, et en coupant avec une pince coupante tout ce qui dépasse.
Liens utiles
- http://wiki.jelectronique.com/realisation_de_circuits_imprimes
- http://alain.canduro.free.fr/circuits.htm
FabLabs et mutualisation des ressources
Les trois techniques présentées précédemment sont très pratiques pour réaliser un prototypage rapide, mais nécessitent toutes un peu de matériel, qui, bien que peu coûteux pour les deux premières solutions, représente au final entre 50 et 300 euros, et prend de la place.
Il peut être intéressant de trouver un FabLab qui dispose de toute ou partie de ce matériel, ou qui serait intéressé pour l'acquérir, libérant de la place chez vous et permettant de mutualiser l'ensemble des coûts, et éventuellement de tester les différentes solution.
La dernière étape est l'application d'un vernis sur la totalité du circuit. Il faut choisir un vernis thermosoudable qui permettra de souder les composants malgré la couche de vernis. Je n'ai personnellement jamais testé, je ne connais pas la tenue des ces vernis et leur comportement lors de la soudure autre qu'au fer à souder.
Services de fabrication en ligne
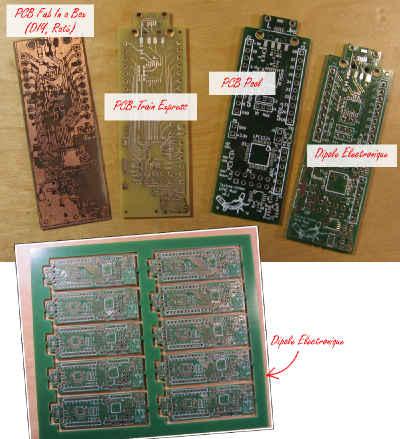
Si vous n'avez pas la fibre DIY jusqu'au bout des doigts, ou que manipuler des produits chimiques potentiellement dangereux ne vous amuse pas plus que moi, il existe des services de fabrication un peu partout dans le monde pour faire fabriquer des circuits imprimés avec une qualité professionnelle (ce sont souvent ceux utilisés par les professionnels) à un coût raisonnable (voir défiant toute concurrence).
Attention, je ne parle pas ici de personnes qui se proposent de faire des circuit imprimés en utilisant une des méthodes citées ci-dessus à votre place, pour un tarif souvent plus élevé que les fabriquant industriels, avec les même délais, et pour une qualité qui n'a rien de comparable avec ce que proposent les fabricants industriels.
Bien entendu, si vous êtes extrêmement pressés et que vous voulez pouvoir tester votre circuit dans l'heure, ceci n'est pas une solution.
J'ai testé plusieurs services de fabrication en ligne, dont PCB-Pool, qui produit en Irelande, Dipoles Electroniques, qui produit en France, PCB Train, qui produit en Angleterre, et Seeed Studio qui produit en chine.
Chaque fabriquant a ses avantages et inconvénients, que je vais essayer de vous présenter, mais qui n'engagent que moi.
- PCB-Pool (https://www.pcb-pool.com) : les plus chers (ou pas), mais avec un réel service ajouté de vérification du circuit imprimé, la possibilité d'envoyer votre circuit au format natif KiCad (pas de possibilité d'erreur sur la génération des Gerbers), et le pochoir CMS en métal découpé au laser ... disons inclus dans le prix de base sur les quantités inférieures à 100 pièces.
- Délai "standard" de 8 jours ouvrés, plusieurs modes de livraison, possibilité de livraison plus rapide en payant plus cher.
- Tarif : 140€ HT pour un circuit de 100mm x 160mm double face, vernis et sérigraphie double face, avec pochoir CMS en délai 5 jours, mais cela passe à 85€ HT sur le délai standard 8 jours avec une seule face de sérigraphie.
- SAV / Support en Français.
- Possibilité de réalisations plus techniques (pistes plus fines, perçages plus fins) ou de délais plus cours (jusqu'à 2 jours).
- Dipole Electronique (http://www.dipole-electronique.fr/) : même service que PCB-Pool, mais l'envoi des fichiers se fait par mail au format Gerber, le format est fixe (ils font les découpes du contour, rassurez vous), et vous avez moins d'options de fabrication sur l'offre "prototypes taille fixe".
- Délai "standard" de 5 jours ou 10 jours.
- Tarif : 60€ HT pour un circuit de 100mm x 160mm double face, vernis et sérigraphie double face, sans pochoir CMS, en délai 5 jours, et 45€ HT sur le délai de 10 jours.
- Pochoir CMS métal en découpe laser : forfait de 70€ HT.
- SAV / Support en Français.
- PCB Train : j'ai été très déçu par leur prestation, lorsque vous sélectionnez les délais rapides il faut lire les petits caractères pour comprendre qu'il n'y aura ni vernis ni sérigraphie, la sélection des produits est globalement incompréhensible, pour un prix équivalent à PCB-Pool sans le pochoir CMS gratuit.
- Seeed Studio (http://www.seeedstudio.com/service/) : Low cost, mais haute qualité. Envoi des fichiers en ligne au format Gerber, et peu d'options (obligatoirement vernis et sérigraphie double face pour les circuits double face), mais vu le tarif, difficile de se plaindre.
- Délai : variable, en général l'envoi se fait sous 5 jours, et possibilité de livraison gratuite si vous n'êtes pas pressés (en dessous d'un certain poids)
- Tarif : à partir de 10$ pour 5 circuits de 5cm x 5cm, prix croissant par pas de 5cm, décroissants en volume (classique) et options payantes (finition, couleur du vernis), pour comparaison, 46$ pour 5 circuits imprimés de 10cm x 15cm
- Pochoir CMS en métal à partir de 70$
- SAV / Support en Anglais.
- Autre avantage : la possibilité de grouper votre commande avec plein de gadgets intéressants ou d'outils ou de matériel de prototypage, comme une pince brucelle à pointe fine pour le placement des composants CMS si vous n'en avez pas.
Il en existe bien entendu beaucoup d'autres, mais je ne les ai pas testés. J'avais trouvé une liste avec des commentaires, mais je ne la retrouve pas.
Personnellement j'utilise PCB-Pool quand j'ai des contraintes spécifiques (délais, taille des pistes et perçages, ou que j'ai besoin d'un pochoir CMS métallique pour une production en série), et sinon soit Dipoles Electroniques pour les productions en série (made in France :) et Seeed Studio quand le budget est serré.
Ha oui, un point hyper important que j'allais oublier pour PCB-Pool : le suivi des étapes de production, avec photo de votre PCB entre chaque étape ... quoi ? je suis le seul que ça intéresse ?
Achat des composants
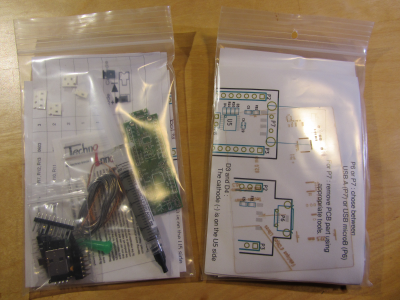
Maintenant que votre circuit est en cours de fabrication, plutôt que de trépigner d'impatience en attendant les informations de suivi de fabrication par email, je vous propose de vous pencher sur la commande des composants (cela vous fera un deuxième sujet d'impatience pour trépigner de plus belle).
Cette étape devrait être rapide si vous avez bien noté les références des composants sélectionnés lors de vos recherches pour la conception du circuit, mais rien ne vaut une ultime vérification. Vérifiez bien les boîtiers sélectionnés (de nombreuses références sont disponibles en plusieurs boîtiers, qu'il s'agisse des condensateurs et résistances (0402, 0603, 0805, ...), des diodes, transistors, régulateurs (SOT-23, SOT363, SOT-223, TO-92, SOD, ...) ou même des microcontôleurs (QFN, TQFP, TSOP, SOIC, ...).
Deux solutions s'offrent à vous. Chercher à économiser chaque centime en écumant les sites de tous les revendeurs de France et de Navare, et payer plein plein plein (plein) de frais de port (après avoir perdu encore plus de temps), ou sélectionner un unique fournisseur au catalogue bien fourni, pour éventuellement avoir les frais de port gratuits car vous commandez plus qu'une certaine somme.
Je n'ai pas d'accords commerciaux avec les différents fournisseurs de composants (pas plus que pour les services de fabrication de circuits imprimés, malheureusement), mais je vous conseillerais tout de même ceux que j'utilise courament, à savoir Farnell, Mouser et DigiKey. Je ne peux que déconseiller Conrad (chers, site mal foutu, et encore plus chers avec un compte pro !) et Electronique Diffusion (qui renvoie vers le site all-datasheets pour les documentations techniques sans donner le fabriquant des composants vendus !!!).
Ma préférence va à Farnell dont j'aime bien l'interface et le système de recherche (et la livraison gratuite le lendemain pour les comptes pro sur le stock Europe), mais c'est une question de préférence personnelle, et il m'arrive de commander chez les deux autres fournisseurs cités quand je ne trouve pas un composant ou quand j'ai besoin d'un gros volume, les réductions en volume étant parfois plus intéressantes (mais pas toujours).
(PS : Dans le cas du module GPIO-Demo, vous pouvez aussi acheter notre Kit.)
... et du matériel
Si vous n'êtes pas équipé, il est aussi temps d'acheter le matériel manquant, il vous sera de toutes façons utile pour plein de projets, il n'y a rien de spécifique.
J'ai dressé une petite liste qui devrait vous permettre de vous en sortir avec votre circuit :
- Un fer à souder. (Je déconseille fortement les fers sans station permettant de régler la température, une station qui tient la route coûtant dans les 60 euros, ce n'est pas un investissement déraisonnable. Lisez l'article sur ce sujet dans le premier numéro de "Hackable Magazine" si vous êtes sceptiques.)
- De l'étain. (Personnellement, je n'ai pas trouvé d'étain sans plomb utilisable, mais vous pouvez essayer.)
- De la tresse à dessouder.
- Une pince coupante. (De préférence avec la ligne de coupe au bord des mâchoires pour pouvoir couper à ras.)
- Une pince brucelle
- Un multimètre (Avec fonction "bip" pour tester la continuité des pistes ... ou les courts-circuits :( )
- Une plancha. (Si si, vous avez bien lu. Tout type de poêle électrique devrait faire l'affaire.)
- Une petite loupe. (Toujours pratique pour vérifier les soudures.)
Masque de soudure
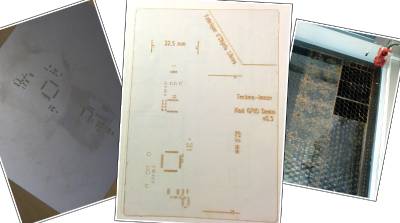
Il y a heureusement une deuxième activité que vous pouvez pratiquer (trépigner ne sert à rien (si si, je vous assure), et ça fatigue (au moins votre entourage)) en attendant vos cartes électroniques (et vos composants maintenant). Si vous n'avez pas commandé le pochoir CMS en métal et que vous choisissez cette solution pour la soudure, c'est la fabrication du pochoir CMS en plastique (à condition d'avoir accès à une machine de découpe laser, mais si ce n'est pas le cas il y a une alternative ... qui vous fera trépigner d'impatience une fois de plus).
Le Pochoir CMS (ou masque de soudure) est habituellement une fine feuille de métal (120 à 175 microns d'épaisseur) qui est utilisée par les fabricants de cartes électroniques pour mettre la soudure sur le circuit imprimé avant le placement des composants et le passage en four pour la soudure. Cette plaque est percée de trous, un pour chaque "pad" de chaque composant CMS, délimitant un volume équivalant à la quantité de soudure nécessaire pour souder la patte du composant sans faire de pâté pour qu'il n'y ait pas de court circuit.
Le soucis du pochoir CMS en métal c'est son prix, impossible d'en inclure un dans chaque Kit du module GPIO-Démo. Il me fallait une solution alternative, et j'ai donc pensé à faire la même chose avec la machine de découpe laser du FabLab de Lyon (La Fabrique d'Objets Libres). Le problème, c'est qu'elle ne peux pas couper le métal, j'ai donc du me rabattre sur le plastique.
L'étape la plus compliquée est de trouver des feuilles de plastique dont l'épaisseur est spécifiée par le commerçant, et de la même épaisseur que les pochoirs métalliques, donc de l'ordre de 150 microns. L'épaisseur est primordiale, car c'est elle qui donnera la quantité de soudure déposée.
Les premiers plastiques que j'ai trouvé avec l'épaisseur spécifiée sont des rhodoids alimentaires (175 microns et 130 microns), mais ils sont difficile à acheter autrement qu'en ligne, et sont souvent de grande taille (60cm x 40cm), donc pas pratiques à manipuler, mais en cherchant bien on en trouve de dimension raisonnable (A4). Et je suis tombé par hasard sur des feuilles plastiques pour premières pages de dossiers (ceux que l'on relie, que l'on doit rendre en quatre exemplaires pour nos projets et qui finiront au fond d'une poubelle dans quelques années^W semaines) dont l'épaisseur est spécifiée sur la pochette : 130 microns, pile ce qu'il faut, et bien moins cher que le rodhoid alimentaire, si ce n'est qu'il faut en acheter 100 feuilles.
Après quelques tests réalisés au FabLab, j'ai fini par obtenir un pochoir plastique très convenable à partir de la couche "Solder Paste" de KiCad, mais il faut cependant faire quelques retouches du fait de la rétractation du plastique quand il est fondu par le laser. Pour obtenir un résultat correct en prenant en compte ce problème de rétractation du plastique qui donne des trous plus grands que prévu, il faut diminuer la taille de certaines pastilles.
Pour le faire, j'utilise Inkscape après avoir exporté la couche "Solder Paste" en SVG. Il faut commencer par dégrouper toutes les pastilles, sans quoi leur position change quand on applique la réduction au groupe. Il faut ensuite ne laisser que les bords, qui seront les traits de coupe, car KiCad exporte des rectangles pleins.
Vous pouvez enfin sélectionner les pastilles "de taille moyenne" pour les réduire de 20 à 60% (selon l'épaisseur du plastique que vous avez trouvé, le type de plastique, et la puissance du laser lors de la découpe, et le type de composant).
Je sais que "de taille moyenne" ne veut rien dire du tout, et je vais donc l'expliquer. Il n'est pas nécessaire de faire de modification pour les grandes pastilles comme les pattes de fixation de connecteurs ou les plans de masse des régulateurs de tension. Passé 3mm x 3mm, il faut laisser la pastille telle quelle. Il en va de même pour les composants en boîtier 0402, car si le trou est trop petit la soudure colle au plastique et reste dans le trou du pochoir quand on le retire, ce qui n'est pas l'effet recherché. Pour tous les autres trous, il faut appliquer une réduction, plus ou moins grande en fonction de la feuille de plastique, mais aussi du type de composant et de l'espacement des broches. Pour les circuits intégrés comme le microcontrôleurs du module, mais aussi l'EEPROM, la porte multifonction, ou le capteur de température, je fais une réduction plus importante (50% à 60%) que pour le reste des composants (20% à 40%), pour limiter ou supprimer les courts-circuits lors de la soudure qui se produisent quand il y a trop de soudure.
Une fois les pastilles réduites (en veillant bien à conserver leur position), vous pouvez ajouter un contour pour que le pochoir se détache de la feuille. Veillez dans ce cas à le faire plus grand que le circuit imprimé, ce qui permettra de le fixer, et faites attention à ne pas faire un contour continu, sans quoi le plastique risque de se replier pendant la découpe du fait de l'aspiration. Pour éviter cela, il suffit de laisser de petits espaces qui rattachent le pochoir au reste de la feuille (moins de 1mm de large), ce qui maintiendra le pochoir pendant la découpe et permettra de détacher le pochoir sans outils, juste en tirant dessus.
Vous pouvez maintenant aller au FabLab le plus proche si vous en avez un qui ait une machine de découpe Laser pour faire votre découpe. Si ce n'est pas le cas, vous pouvez demander à un FabLab qui en a une, si ils peuvent vous faire la découpe en leur envoyant le plastique et une enveloppe timbrée pour le retour, avec un petit quelque chose pour le travail, négocié avec eux au préalable (et tous les FabLab de France qui ont une découpe Laser vont me maudire). Ou bien utiliser les services de Pololu, qui proposent cette solution depuis quelques temps, soit parce qu'ils ont fait le même constat et eu la même idée que moi, soit parce que mon idée a voyagé (laissez moi croire en la deuxième solution svp), même si ils proposent ce service un peu cher à mon goût. http://www.pololu.com/product/446
Et enfin, avant d'utiliser le pochoir, je le "racle" avec une règle métallique pour enlever les surépaisseurs de plastique sur les bords des trous, du fait de la rétractation du plastique pendant la découpe.
Vous voila avec un (joli) pochoir CMS à moindre frais (en tout cas normalement bien moins de 70 euros), même si il ne tiendra pas des centaines d'utilisation, et ne peux pas être nettoyé à l'acétone. J'en ai utilisé certains une dizaine de fois, et je me sers d'une petite épingle pour nettoyer les restes d'étain une fois sec.
Assemblage
Après quelques (trop nombreux) jours d'attente, vous avez enfin reçu votre circuit imprimé et vos composants, et vous allez pouvoir attaquer la suite des réjouissances :)
Bien entendu, il existe des sociétés spécialisées dans la réalisation des étapes suivantes pour des prototypes, mais les coût sont souvent non négligeables, et le résultat pas toujours au rendez-vous (composants inversés, mal soudés, ...). A noter que certaines sociétés de fabrication de PCB proposent ce service ... à condition que vous utilisiez un logiciel propriétaire pour envoyer les données d'assemblage :(
Dépose de l'étain
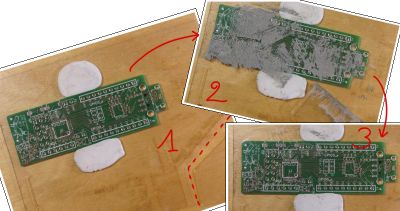
Mais attention, ne vous précipitez pas, il faut commencer par un petit check-up, il est encore temps. Avant de mettre de l'étain plein partout, vérifiez que vous avez bien reçu tous les composants, que vous n'en avez pas oublié, et que les empreintes correspondent bien. Il est encore temps de commander les références manquantes, en revanche, une fois l'étain appliqué avec le pochoir, il commence à sécher, et même si il est toujours possible de positionner les composants plus tard, c'est bien plus sympa quand ils "collent" dans le "gel" qui compose l'étain "en pâte" (ou crème à braser, ou étain "liquide", qui n'est autre que des micro billes d'étain dans un gel).
Vous avez tout ? Bien. Pas d'erreur de miroir sur les pattes des composants ? Parfait ! (Et oui, c'est du vécu).
Mais avant de vous lancer, un dernier préparatif : vérifiez que vous avez accès à un schéma de votre carte, pour pouvoir placer les composants au bon endroit une fois l'étain déposé sur le circuit.
Note : Pour ceux qu'un texte et quelques photos ne sauraient contenter, j'ai fait une vidéo de l'assemblage du module GPIO Demo, voir le lien en fin d'article.
Vous pouvez enfin attaquer les choses sérieuses, et dans une petite heure (ou moins, parce que vous êtes très fort) vous aurez votre nouveau jouet rien qu'à vous.
La première étape, dégraisser le circuit imprimé, pour que le gel adhère bien. Frottez le légèrement avec un chiffon non abrasif et un peu d'alcool, sans insister (normalement les circuits arrivent relativement propres, mais nos doigts ne le sont pas toujours).
Ensuite, le plus simple pour fixer le circuit pour l'application de l'étain avec le pochoir (ou tout autre méthode en fait) c'est la "patafix" (ou tout équivalent, je n'ai pas d'actions non plus). Cette matière semi collante permet de maintenir en même temps le circuit imprimé et le pochoir CMS que vous allez devoir aligner correctement. Pour cette opération, le pochoir en plastique transparent offre un très net avantage sur son homologue en métal opaque, mais on s'en sort dans tous les cas. Veillez à ce que la patafix n'empêche pas le pochoir d'être parfaitement plaqué au circuit imprimé.
Déposez un (tout petit) peu d'étain sur le pochoir (si vous avez de l'étain en seringue c'est plus pratique), et étalez le avec une spatule (j'utilise un morceau de pochoir métallique découpé dans un vieux pochoir inutile, et j'ai mis un morceau "prédécoupé" sur les pochoirs en plastique du kit du module GPIO Demo, mais n'importe quel morceau de plastique avec un bord droit fait l'affaire). Appuyez bien sur le pochoir pour qu'il reste plaqué au circuit pendant toute l'opération, mais sans le faire bouger. Remplissez bien tous les trous, puis raclez l'étain qui est en trop, pour qu'il ne reste que la bonne quantité d'étain dans les trous.
Vous pouvez maintenant passer au plus délicat, retirer le pochoir sans le faire bouger, et en laissant l'étain sur le circuit imprimé. Ne paniquez pas, vous pourrez recommencer plusieurs fois si besoin. J'ai constaté que pour bien laisser tout l'étain sur le circuit il faut retirer le pochoir en le pliant, comme si il s'enroulait autour d'un rouleau.
Vérifiez bien qu'il ne reste pas (ou presque) d'étain dans les trous du pochoir, et si vous êtes satisfaits du résultat vous pouvez passer à la suite. Vérifiez aussi que l'étain ne se soit pas glissé sous le pochoir pendant l'application pour former de gros pâtés. Sinon, nettoyez le pochoir (sommairement) et recommencez à l'étape ... un peu plus haut quoi.
Placer les composants
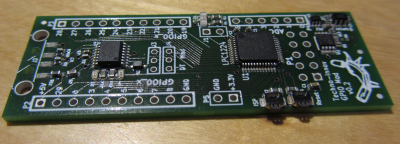
Il ne vous reste que quelques étapes, mais celle-ci est peut-être bien la plus minutieuse, et la plus longue.
Vous allez maintenant pouvoir placer les composants CMS sur votre circuit. Attention, ne placez pas les composants traversants, ils gêneraient pour l'étape suivante.
Personnellement je préfère commencer par les petits composants, car ils collent au gel quand celui-ci est bien frais, et ne bougent plus quand on tourne ou déplace le circuit imprimé. Pour ce faire, j'utilise une pince brucelle avec une pointe très fine, mais une simple pince à épiler peut faire l'affaire.
Une fois le composant positionné correctement, c'est à dire avec toutes les pattes ou les extrémités au dessus d'un plot de soudure, j'applique une petite pression sur le composant pour qu'il colle bien au gel et ne bouge plus par la suite. Cela évite notamment les composants qui se déplacent pendant que l'étain fond et se retrouvent en l'air, soudés par une seule patte ou d'un seul côté.
Attention à ne sortir qu'une référence de composants à la fois, ils sont tellement petits qu'il est difficile de lire les références sur les composants, ou même n'ont pas de références imprimée du tout (les condensateurs et les inductances par exemple).
Attention aussi au sens pour les composants polarisés (diodes, leds, certains condensateurs) ou avec plus de deux pattes. Il y a le plus souvent un indicateur, parfois sous le composant (pour les leds), parfois difficile à détecter, et il faut alors se référer à la documentation technique (ou utiliser une loupe, ou les deux).
Continuez avec les références suivantes, pour finir par les plus gros composants, que je place en dernier pour qu'ils ne gênent pas pour la pose des autres composants, mais aussi parce qu'une fois que le gel a un peu séché il est possible de bouger le composant sans déplacer l'étain, et de ne le "faire tenir" par une petite pression que lorsque le positionnement est bon.
Allez, plus que quelques composants à placer, courage ! (Oui, on a créé des machines pour ça, mais elles ne sont pas dans nos budgets).
Soudure CMS
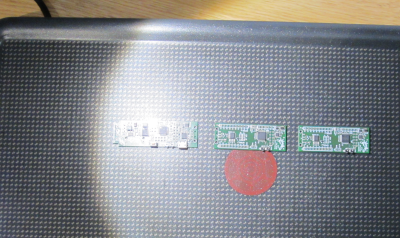
Passons aux choses sérieuses : sortez la plancha !
Pour souder des composants CMS il existe différentes méthodes, mais si l'on en croit les tests que l'équipe de Sparkfun a réalisé le plus efficace c'est la plancha (ou toute surface chaude équivalente : poêle électrique, machine à crêpes, ou même une vieille poêle sur le gaz (attention aux problèmes conjugaux ...)).
Cette étape est la plus simple : on pose le circuit imprimé sur la plancha (composants sur le dessus bien entendu), on la branche, et on attends. C'est aussi la plus dangereuse : la plancha va atteindre plus de 250°C ! Gare aux brulures, à ne faire qu'accompagné d'un adulte (responsable ? ça existe ?). En fonction de la puissance de la plancha, cela dure entre 2 et 5 minutes, et l'étain se met à fondre, soudant les composants. On voit très bien quand l'étain fond car il devient brillant.
Une fois que le processus a commencé, cela va très vite, et il ne faut pas insister si quelques points ne veulent pas fondre tout de suite, car les autres composants sont entrain de cuire. Il faut retirer la carte de la plancha tout de suite, en faisant bien attention à la garder à l'horizontal car ils ne sont plus tenus en place par le gel. Si vous inclinez la carte à ce moment la, les composants vont glisser (Il faut entre 4 et 10 secondes à l'étain pour solidifier). Pour cela les plancha sont bien pratiques car elles ont généralement une zone sans rebord, ce qui permet de faire glisser la carte vers le bord et de la saisir avec une pince avant de la déposer sur une surface protégée (surtout pas sur du plastique, elle est autour de 200°C !)
Ça y est, c'est fait, c'est soudé ! Enfin ...
Reprise des faux contacts
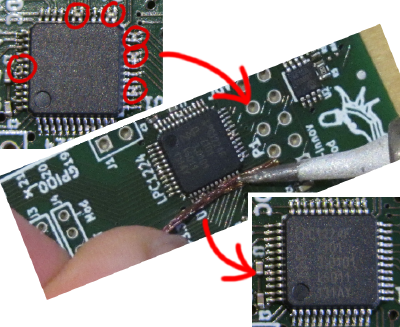
Bon, en théorie, tout c'est bien passé et il n'y a pas de faux contacts. Malheureusement, même avec un pochoir CMS métallique certaines pattes de circuits intégrés peuvent être reliées par de l'étain si il y en avait un petit peu trop.
Dans ce cas là, pas d'affolement, la première chose à faire : ne surtout pas prendre le fer à souder ou remettre la carte sur la plancha. La première étape est de reprendre le schéma de la carte.
Et oui, j'ai parfois passé près d'une demie heure à tenter d'enlever la soudure qui faisait contact entre deux pattes ... reliées par un fil sur le schéma.
Si effectivement le schéma dit qu'il ne devrait pas y avoir de contact, utilisez la tresse à dessouder et le fer pour enlever le surplus d'étain, en mettant un morceau propre de la tresse à dessouder entre l'étain à enlever et le fer à souder. Testez avec le multimètre pour vérifier que le court-circuit a bien disparu.
Il faut aussi finir de souder les composants des bords de la carte qui n'auraient pas été soudés sur la plancha. Pour ceux-ci, pas besoin de rajouter de soudure, il suffit de poser le fer à souder (chaud) très proche de la pastille (ou sur la pastille) pour que l'étain fonde et soude le composant.
Profitez-en pour vérifier que tous les composants sont bien soudés des deux côtés.
Attention, vous pourrez avoir l'impression que certains composants sont mal soudés ou qu'il n'y a pas assez de soudure car la quantité de soudure utilisée avec cette méthode est très faible et que la soudure ne forme pas de pâté. C'est normal. Pour vous rassurer, vous pouvez utiliser la même méthode que pour finir de souder les composants dont l'étain n'avait pas fondu à la plancha. Vous verrez alors l'étain briller un peu plus, et re-solidifier lorsque vous retirez le fer.
Soudure des composants traversants
Avant dernière étape avant de jouer avec votre circuit : souder les composants traversants, et éventuellement ajouter de la soudure sur les pads de fixation des gros composants et des connecteurs.
Pour cela rien de magique (quoique, voir l'astuce qui suit). Mettez en place le composant (attention au brochage si il y en a un), positionnez votre fer à souder en contact avec le circuit imprimé et la patte du composant que vous voulez souder, puis apportez la soudure, et retirez la soudure et le fer (dans cet ordre).
Petite astuce : utilisez de la patafix pour maintenir le composant en place et pour maintenir le circuit sur le plan de travail. Depuis que j'utilise cette technique ma troisième main sert de support aux toiles d'araignées ...
Tests
Dernière étape avant de passer à la programmation, qui fera l'objet du prochain article : les tests électriques.
Ne mettez pas votre circuit sous tension tout de suite, certains composants ne tiennent pas longtemps en cas de court circuit, même alimentés par l'USB.
Utilisez le multimètre pour vérifier qu'il n'y a pas de court circuit entre le +5V et la masse, entre le +3V et la masse, et pour ne pas risquer d'endommager les ports USB de votre PC/HUB (certains sont très fragiles), vérifiez aussi entre les deux pistes USB (D+ et D-) et la masse et le +5V.
Si vous n'êtes pas trop impatient, vous pouvez aussi tester entre chaque pattes consécutives des circuits intégrés, mais vérifiez bien le schéma en même temps, toujours pour éviter de passer des heures à vouloir enlever un court-circuit qui n'en est pas un.
Tous est bon ? et bien c'est fini pour cette fois.
Si vous avez réalisé le circuit du module GPIO Demo, vous pouvez le connecter sur un port USB de votre PC.
Le microcontrôleur doit se mettre automatiquement en mode programmation (ISP) et la led bicolore doit faire apparaitre deux point lumineux très très faibles (vert et rouge).
Si votre noyau a bien le support FTDI (suffisamment récent pour avoir le composant FT230XS, plus récent que 2.6.28 de mémoire), vous aurez alors un nouveau ttyUSB (présent dans /dev/, et annoncé dans les logs du noyau), et en envoyant le caractère '?' le microcontrôleur devrait répondre "Synchronised".
Rendez-vous dans l'article suivant pour l'écriture du code en C, la compilation, et la programmation avec l'utilitaire lpcprog :)
+++
Liens
FabLabs :
- ElectroLab de Nantère
- Fabrique d'Objets Libres (FabLab de Lyon)
Informations sur la fabrication de circuits imprimés :
- http://wiki.jelectronique.com/realisation_de_circuits_imprimes
- http://alain.canduro.free.fr/circuits.htm
Fabricants de circuits imprimés :
Module GPIO Demo :